大量生産には、最先端の設備と高度な管理システムを備えていなければならない。しかし、そこからさらに製品の完成度を高めていくのに必要なのは、やはり人の手作業と感性ということになる。宮崎ソーイングでは、あらゆる工程に技術を継承しているプロフェッショナルがいることが、ダーバンの安定した品質を生み出しているのだ。
工場内に足を踏み入れ、まず感じたのは、常に一定の室温と湿度に保たれていること。猛暑の中、汗だくで工場に到着したが、一瞬にして汗が引いていくのがわかる。熱を発する機械が多数あるなかでは、空調にかかるコストアップにつながる。それでも「スーツの品質のため」という並々ならぬ思いを、温度設定からも感じることができた。そして見学を進めるにつれ、その思いをまさに働くスタッフからもひしひしと感じとることになる。
生地の品質をチェックする、人の目
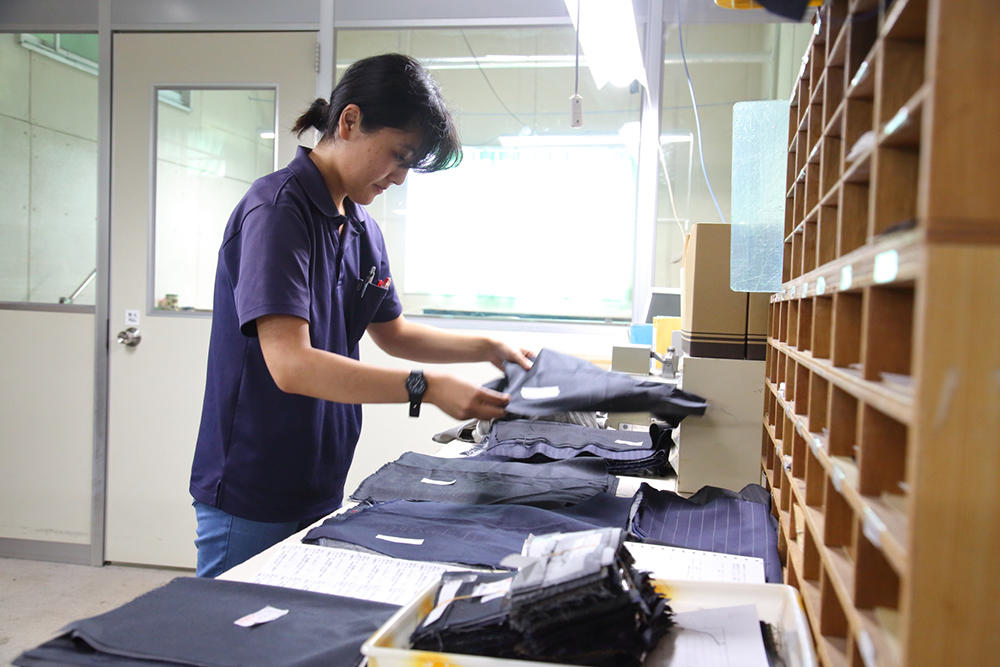
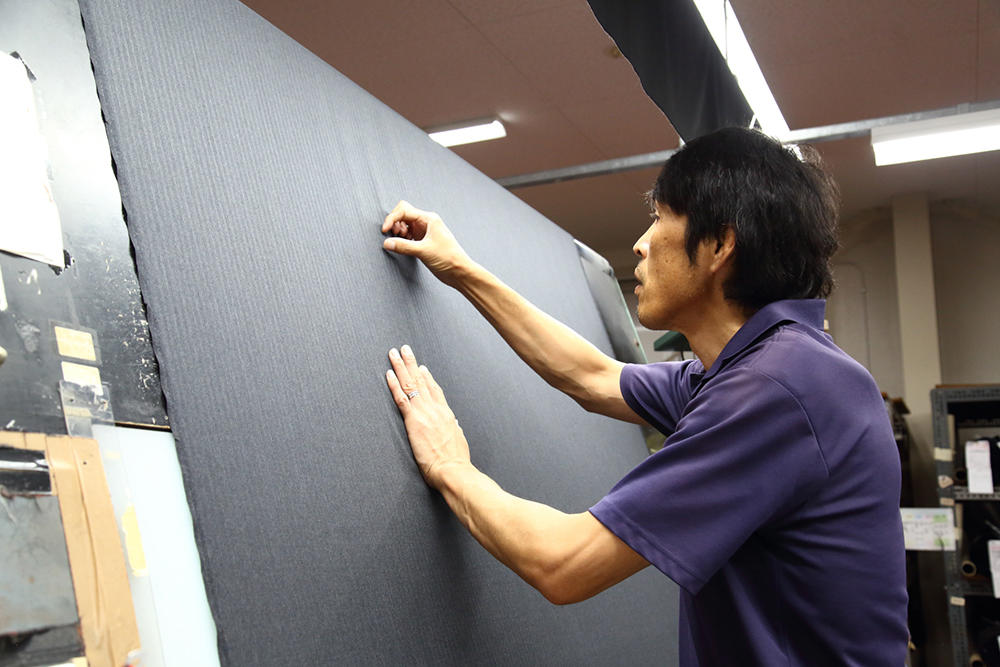
スーツができあがるまでの工程は、大きく分けて試験室、検反作業、裁断、縫製、仕上げ、最終検査の6つ。
試験室、および検反作業では生地の品質検査や織り傷が含まれているかなどを確認する。
さまざまな機械により、生地の伸縮や滑脱、寸法変化率、風合いなどの検査が行われる。生地は原毛や織り方などによって特徴が異なるからだ。もっといえば、ヨーロッパの高級生地をそのまま日本に持ち込んでも、気温や湿度の違いによって、思わぬヨレや縮みが発生することがある。その違いを数値化することにより、スーツ作りに適合する糸や芯地、裏地など、使用素材の参考にするのである。この検査機能を自社で所有しているブランドはほとんどないといっていい。日本で既製品のスーツを最初に作ったダーバンだからこそ、継承し続けてきた機能なのだ。
工場のスタッフは、年齢層の高い超ベテランばかりかと思っていたが、意外にも老若男女がバランスよく配置されている。それを表すかのように、生地試験もベテランのおじさんがこめかみにシワを寄せてしているのを想像していたのだが、実際は20代の女性が淡々と行なっている。だが、そうした若いスタッフも膨大なデータを蓄積しており、検査のプロフェッショナルなのだ。技術と経験の継承が滞りなく行われているのが宮崎ソーイングの強みの一つだ。
裁断のためのピン打ちと最初にスーツの形ができあがるアイロン作業
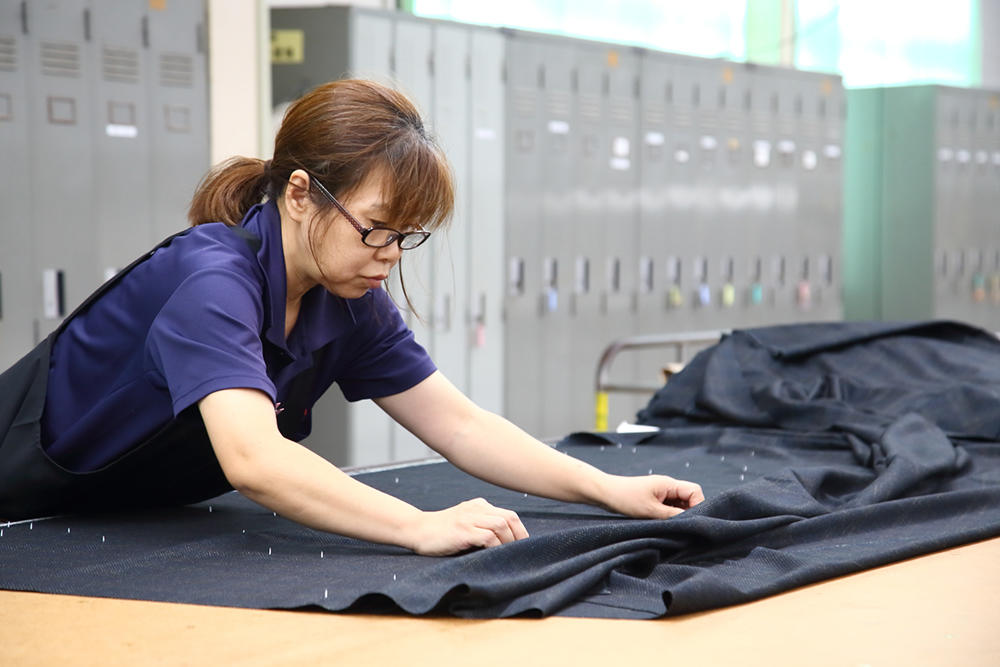
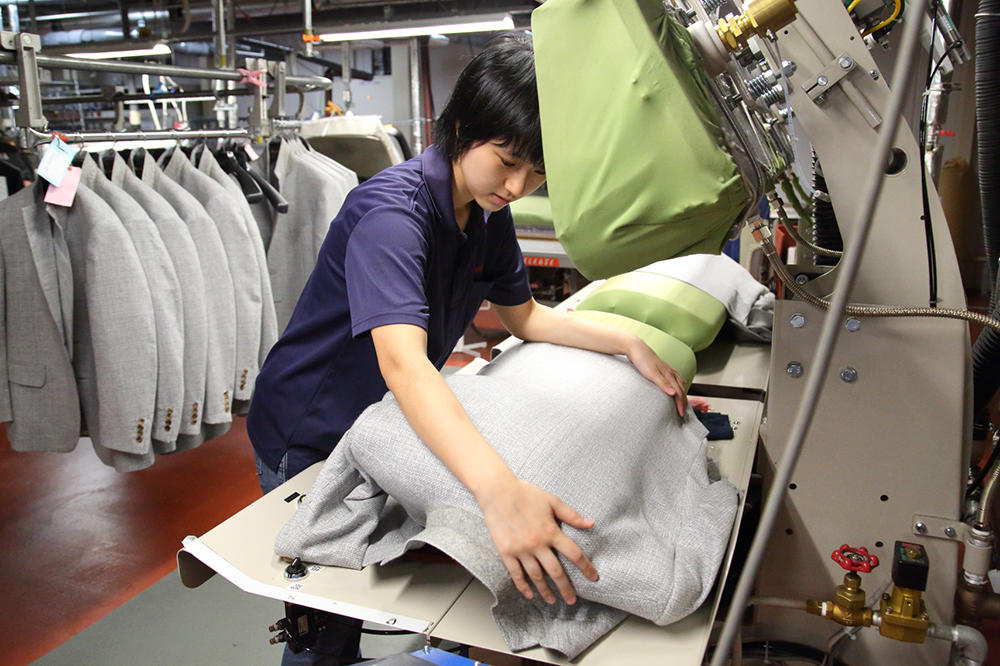
裁断の工程では、生地メーカーより送られてきた生地を一度加湿をして柄合わせをし、微妙にたわませて、重ねていくのがプロの技。紙を10枚ぐらい重ねて切ると少しずつずれていってしまう。それと同じことが起きないように調節するのが人の仕事だ。正直、作業見学していても、何が正解で、何がNGなのか素人には違いがまったくわからない。というのも、生地の特性を見て、たわみの微差を調節するのは経験からくる勘だからだ。この裁断の妙が、最終的にはスーツの立体感へとつながる。
同じ敷地内にある協力工場による縫製過程が終了したら、いよいよダーバンらしさを作っていく工程が始まる。日本人の体型にフィットした丸みのあるシルエットに形成するため、スーツの各パーツ毎に分かれてアイロン工程を行うのだ。このずらりと並ぶアイロンの行列は圧巻だ。ハンドアイロンだけではなく、プレス機と呼ばれる大型のマシンの並ぶ様は、まるでロボットを作る工場のように思えて、そうではないとわかっていても胸が高鳴る。
メーカーによってはアイロンを2ラインで行なうそうだが、宮崎ソーイングでは、プレス機、ハンドアイロン、補修の3ラインだ。素材の柔らかさ、仕立ての種類、肩パットの有無などで、プレスの加減が異なるもの。ゆえに各工程での仕上げが適切になされているかチェックをし、足りない部分には再度細かくアイロンを当て直す作業をするのだ。何十機も並ぶアイロン作業はすべて人力、アナログ。こういったところにこだわるからこそ、仕上げに差がつくのだ。
仕上げ工程では、ベテラン職人による厳しいチェックと仕上げが待つ
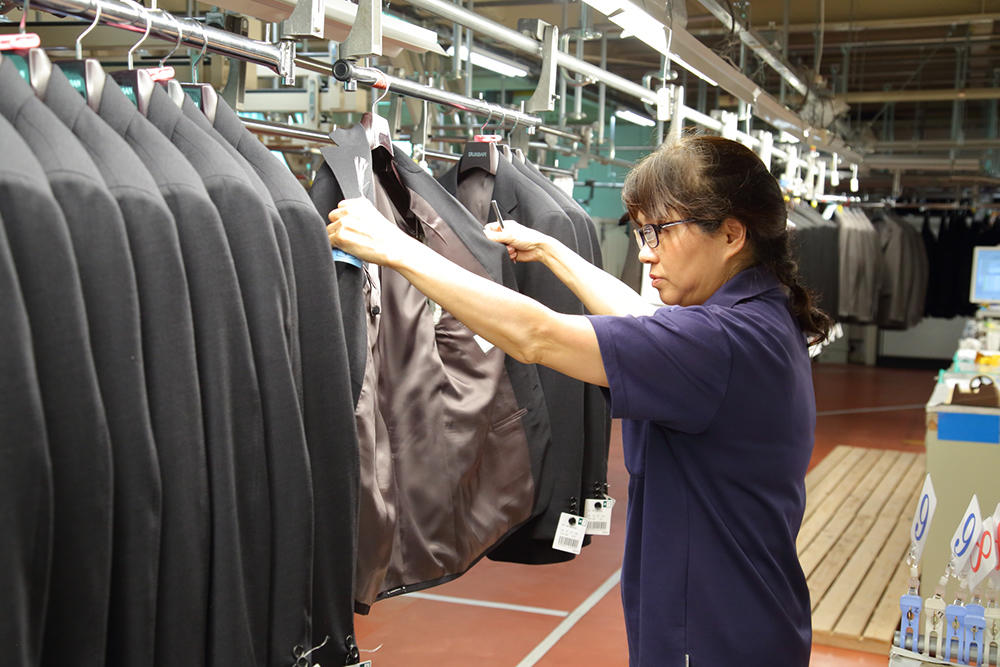
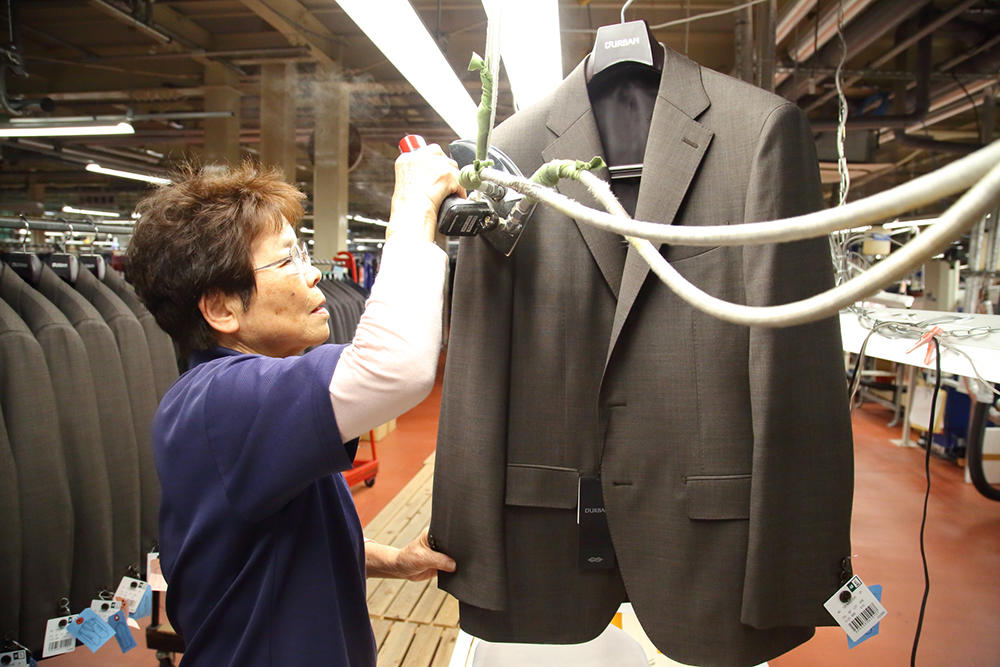
スーツ作りの最後の工程が最終検査だ。ここには各工程別に技術の資格を取り指導にあたるマイスター(下記コラム参照)とは異なる、“匠”が存在する。一点一点厳しい目でチェックをし、素人には分からないような微妙な具合を修正していくのだ。これがスゴイ! わずかな機械の油汚れも見過ごさず洗浄し、わずかな生地の織り傷があればその糸をかがり直して生地自体を修正することもあるという、まさに職人芸。もちろん縫製不良があれば、その場で縫い直し、アイロン不足もその場で行う。各部署や縫製に戻すより短時間で早いうえに、匠たちの高い技術力のフォローアップが十二分に発揮される場面だ。
いいスーツを仕立てるには、それを構築するための素材選びと形作りが欠かせない。パターンのバリエーションや縫製技術はもちろん重要だが、それを形として実現するのが仕上げと最終検査の工程なのだ。こういった匠たちがいるからこそ、既製服と同じ製造ラインで、パーソナルオーダーひとつひとつの細かい注文に対応することも可能になるのだ。ダーバンのスーツは、メンテナンスとして、工場に戻して新品同様に仕上げるプレスサービスを行っている。自社の工場だからこそできるクオリティの高いサービスにもブランドの歴史と心意気を感じることができる。
今回の取材でわかったのが、大量生産の工場とはいえ、ひとつのスーツにこれだけ多く人の手が介在していたこと。一人がスーツ作りのすべてを担うなら、一人の匠がいればいい。だが、量産するにおいては、その工程毎にクオリティを下げることなく、プロフェッショナルを用意する必要がある。スーツ作りは洋服作りのなかでも一番難易度が高く、工程も多く、手間がかかるもの。それを網羅する各部門のプロがいること、さらに管理、指導し未来に繋げ教育していくということは並大抵のことではない。ダーバンの蓄積された膨大な技術とデータは、日本のスーツ文化の資産だとはっきり言える。それをもっと多くの人に知って欲しいと感じずにはいられなかった。
若き技能者を育てるマイスター制度とは?
次世代を担う若きマイスターたち
坊主山の裾野に広がる広々とした工場
ダーバン宮崎ソーイングでは、2008年より優れた技能を持つスタッフの育成及び技術の継承をするために、マイスター制度を導入。裁断、縫製、仕上げなど各工程に分類し、年に2回の試験を行い技術の向上と人材の育成に力をいれている。
なかでも、上衣の縫製、下衣の縫製、仕上げ部門と3つのマイスターを取得しているのが酒元さん(写真中央)だ。「なぜ3つも?」とたずねると、「会社から技術指導をするようまかされたとき、部署をまたいで全般を指導しなければいけないと感じて複数のマイスター取得に挑戦することにしました。そのおかげで課題共有を多くの部署で横断的にできるようになり、技術だけではなく、チェック機能としての指導の重要さも理解するようになりました」と酒元さんは語ってくれた。この若手社員たちのマイスター挑戦へ意欲が、技術向上の励みにもなり、技術のひとつひとつがダーバンの技の継承に繋がっていくのだ。
text:Mariko Ikeda
photograph : Naoki Matsukuma